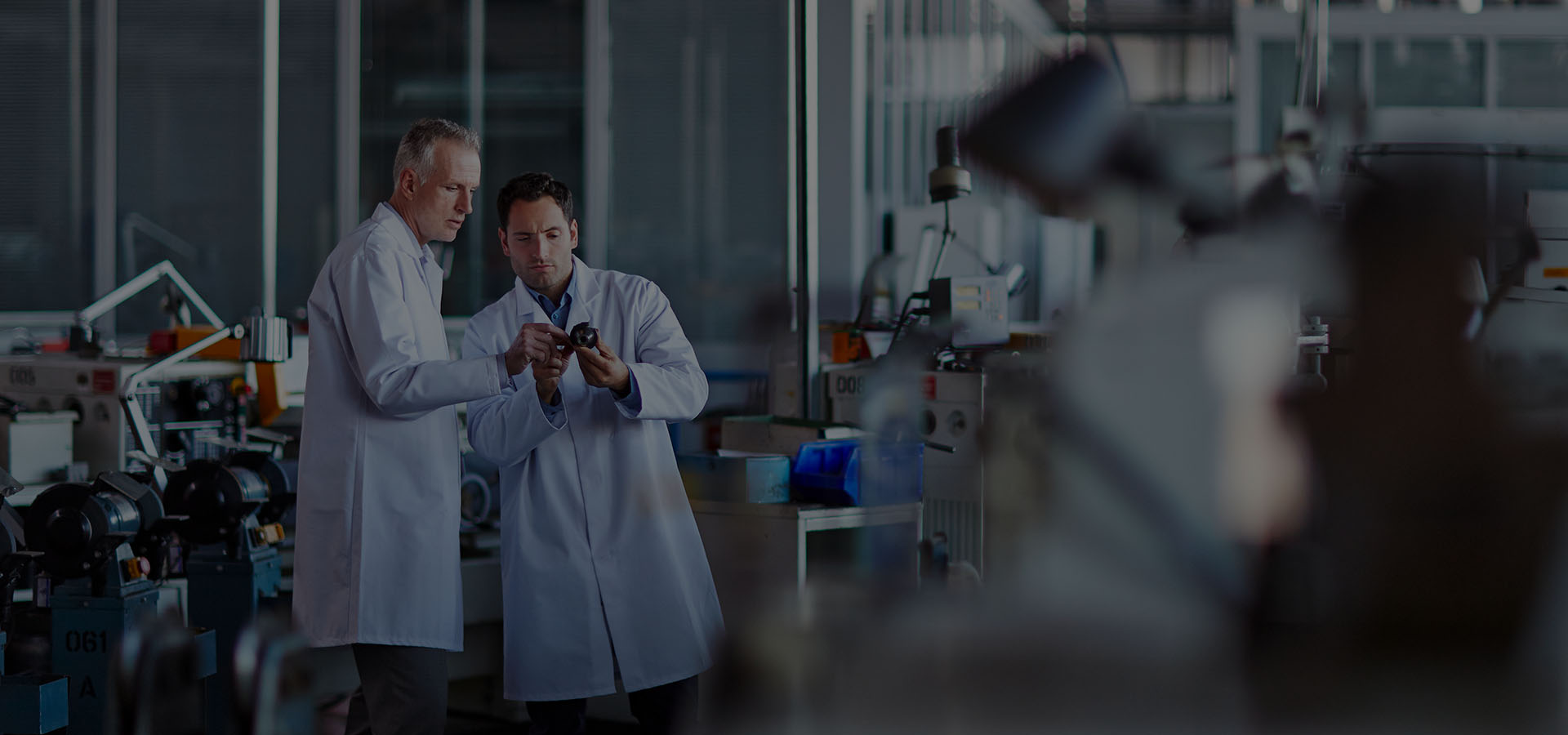
QAD EQMS
(Enterprise Quality Management System)
Manage your product quality with a preventative approach. Optimize manufacturing performance, comply with industry standards and manage risks.
- Improve operating margins
- Delight customers and win new business
- Minimize costs through proactive quality
- Provide accurate data for human and artificial intelligence
Key Challenges
Global trade disruption - rapidly shifting import and export tariffs creates tension that risks breaking critical processes
Explosive AI growth - executives feel competitive forces to increase AI but lack the digital ecosystem needed to scale data-driven insights
Increasing manufacturing complexity - Complexity increases likelihood of quality issues and recalls; up front prevention is the only real solution.
Scarcity of skilled workers - Loss of your experienced workers and their knowledge drives the need to institutionalize knowledge, reduce employee effort through process efficiencies, and have visibility and management of employee training.
Capabilities
- Quality prevention
- Best-practice workflows
- Deep supplier access
- Complete integration
Benefits
QAD EQMS is a fully integrated enterprise quality management system that provides timely visibility into manufacturing and quality-related issues across the enterprise. It facilitates a preventative approach that helps to build quality into the process from the product design phase. Some key benefits include:
Improve customer satisfaction by increasing the number of quality products delivered in full and on time
Improve margins/EBITDA by reducing internal failure costs, preventive quality costs, shipments impacted by quality and recalls
Enhance supplier performance by ensuring conformance to best practices for supplier quality, delivery and continuous improvement and by increasing visibility
Improve collaboration and visibility within the organization and across the supply chain, providing a single source of quality information
Reduce waste due to fewer defects and overproduction, and less waiting, non-utilized talent, transportation, inventory, motion and extra processing
Close training gaps that arise due to retirements, absenteeism and high turnover
Manage and mitigate risk with a closed-loop, integrated system to move your organization from a reactive, costly business model to a culture of prevention
Solution
QAD EQMS helps manufacturers manage quality from end-to-end and allows global enterprises to optimize manufacturing performance, comply with industry-specific quality standards and facilitate risk management analysis. It ensures suppliers comply with quality standards, tracks corrective actions and supports continuous quality improvement. Key capabilities include:
Document Control ensures your team is always working with the latest revisions. Electronic document routings and approvals keep the process moving efficiently and make sure information is available to everyone at the right time.
Training Management helps ensure training needs are effectively identified and addressed, even as changes occur in your organization. It includes comprehensive training tracking capabilities that meet requirements such as ISO 9001, IATF 16949, ISO 13485, HACCP, 21 CFR (QSR) Part 820 and others.
NCR/CAPA (Non-conformance and Corrective Action) capabilities ensure that your company’s dedication to problem resolution has full support for these critical functions, including the ability to start NCRs and CAPAs separately with the option to link when appropriate. Incident Investigations also enable system-driven discoveries as preceding activities to qualifying an event as an auditable issue or address environmental health and safety (EHS) events.
Auditing/LPA (Layered Process Audits) simplifies the entire audit process with a closed-loop system to address product, process and system audits, plus manage any findings or non-conformities.
Risk Management helps prepare risk assessments to identify issues, define the likelihood and consequences, document current controls, and develop treatments to mitigate risk to your organization. It supports the prioritization of risks, ensures mitigation plans are in place and maintains a risk register in a single repository.
APQP (Advanced Product Quality Planning)/Design Control is an essential part of automotive industry standards and the commercialization of medical devices. By taking the time to design for quality and manufacturability, product and service quality improves, and costs are minimized for the life of the product. QAD EQMS provides capabilities to ensure product introductions happen on time and products meet design goals.
PPAP (Production Part Approval Process) is crucial to ensure that the product you receive or ship meets the stated customer requirements. It is also a key part of many certification standards, including IATF 16949. Manage this process with the QAD EQMS system that is fully integrated to APQP and other key processes.
Inspection and SPC (Statistical Process Control) captures process information in a central repository to enable rapid evaluation of the data. The output can be presented quickly in SPC charts that spur effective course corrections.
Complaint Management provides a complete system integrated to CAPA so you not only record complaints but also ensure the situation is resolved effectively.
Adverse Events capabilities ensure that your company’s dedication to adverse events tracking and problem resolution.
Supplier Quality includes supplier quality management that helps ensure conformance to best practices, and supports the planning, execution and documentation of supplier audits.
Continuous Improvement incorporates continuous improvement suggestions, projects, lessons learned, issue management and meetings into a centralized system to manage this crucial process.
Gauge Management monitors gauges with a complete calibration and Measurement System Analysis (MSA) tool kit and ties gauges to inspections and corrective action.
Easily integrate with other systems using either SOAP or REST protocols/APIs.
Brunswick Boat Group Accelerates 4.0 with QAD EQMS
The largest manufacturer of recreational boats in the world, with operations in 30 countries, depends on QAD EQMS to drive faster results across their enterprise.
Imaging systems leader Analogic sees clear value with QAD EQMS
QAD EQMS goes beyond audit confidence in Analogic’s complex regulatory environment by providing operational efficiencies and sustainability improvements.
QAD EQMS improves global operations for PennEngineering
QAD EQMS provides quality standardization and visibility across the global operations and facilities as the industrial fasteners organization grows.
Saft improves production and streamlines audits with QAD EQMS
The high-tech batteries company benefits from QAD EQMS with consolidated systems, greater transparency, lower costs and reduction in errors.
Cascade Engineering improves operations with significant time savings by upgrading to QAD EQMS
QAD EQMS allows the automotive supplier specializing in plastic injection molding to effectively manage quality, proactively manage risk, save time and increase productivity.
Quality Management Software Evaluation
Take advantage of the no-cost QAD EQMS Business Case Analysis to start turning cost leaks into margin improvements.
Further Information
QAD EQMS brings us the ability to problem solve faster because we have data at our fingertips...it speeds up our problem solving. It helps us drive a tremendous amount of improvement.
Brian Hines - VP of Operations, Brunswick Boat Group
How Can We Help You?
Are you interested in exploring QAD Adaptive Applications? Do you have specific questions, comments or feedback? Get in touch with us!
Thank you for reaching out to QAD! Your inquiry has been forwarded to the appropriate representative who will contact you shortly.
In the meantime, for more information on how we can work together toward building an Adaptive Enterprise please subscribe to the QAD Blog for commentary on the latest news and announcements from QAD and the industry.
If you would like to change your message settings, visit our Subscription Preference Center.