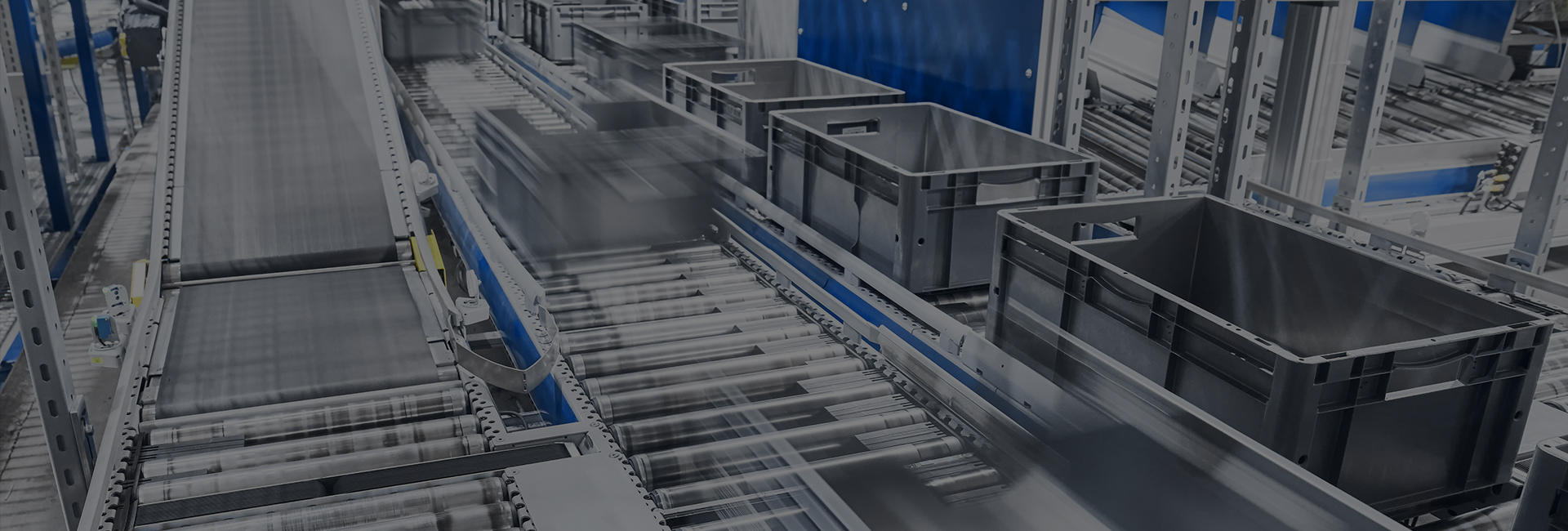
QAD Advanced Scheduling
Your organization needs to optimize production agility and resilience by easily deciding what products to make and accurately sequencing your lines to:
- Eliminate inefficiencies and improve utilization
- Minimize setups, changeovers and overtime
- Enhance customer service
- Increase throughput rates
- Improve decision making when unforeseen disruptions occur
Key Challenges
Supply chain volatility - Producing the right products at the right time efficiently and effectively is complex with the new norm of supply chain disruptions
Increasing customer expectations - Your customers now expect and demand rapid and on-time deliveries to ensure a positive customer experience
Sequencing - With the high frequency of unpredictable production disruptions, it is essential to be able to swiftly schedule and reschedule your operations as needed
Capabilities
- Scheduling optimization
- Plan alignment
- Capacity alerts
- Changeover configuration
Business Alignment. Optimize production by deciding what products to make on each line and in the best sequence to minimize changeovers, balancing working capital, service and cost objectives.
Visibility. Anticipated constraints, such as critical material availability, insufficient team members, insufficient capacity, or exceeding warehouse space are accessible to users.
Aligned Product Wheels™. Define the optimum sequences, cycle times, frequencies, and inventory targets for each SKU. Generate schedules that are aligned with your business’s customer service, throughput and inventory goals.
Scheduling automation. Production sequences can be automatically generated. The Product Wheel Design facilitates optimized rescheduling when dealing with disruptions.
Scheduling analysis. Your schedulers can quickly analyze and create new schedules in seconds to efficiently reschedule and see the time and cost impacts.
Simulation. Conduct “What-If” simulations to identify your optimal operating strategy. Use goal seeking simulations to recommend safety stock levels that support cash, cost and service targets. Consider all factors such as frequencies, lot sizes, demand and supply variability and fill rate targets.
Cycle Time Optimization. Cycle times balance the cost of changeovers and inventory, and frequencies accommodate high and low volume products.
Production Rhythm. Cycle times are harmonized to ensure repetitive schedules are practical and well accepted by plant personnel.
QAD Advanced Scheduling impressed us with its ability to optimize production sequences, minimize changeovers and provide real-time insights. This aligns perfectly with our vision of continuous improvement and operational excellence.
Director of Business Transformation - Mary Ann’s Specialty Foods
Further Information
お気軽にご相談ください
QAD Adaptive Applicationsについてお問い合わせください。
QADへお問い合わせいただきましてありがとうございます。担当者からご連絡を差し上げます。急ぎの問い合わせの場合は各国のQADオフィスへ直接問い合わせください。QADやERP業界からの最新のニュース、および発表に関する解説については、QADブログをご購読ください。<br>
もしメッセージ設定を変更したい場合は、"Subscription Preference Center'"へアクセスしてください。<br>
各種SNSもぜひフォローしてください。